|
 |
The RL28 Storyby Rob Legg |
Episode 1: Designing the RL28
|
Note: I offer no apology for using Imperial measurements as at the time, that was the system in common use, and the description of some materials
refers directly to this .eg. 11,000 grey cast iron refers to a cast iron that has a 11,000 lbs to the square inch tensile strength; rope, wire and
fibreglass etc were referred to in this way.
For years I had put off building the RL24 as the general opinion was that a 24ft boat would be far too big to handle on and off a trailer, when
this assumption proved wrong we planned a maximum sized boat that would fit within the existing road rules for car towed trailers
This sounded simple enough, but we then found that there were no less than five sets of differing rules within Australia, so we worked out a
compromise covering them all, and in the end came up with a practical length limit of 28ft and a maximum load width of 8ft 4in.
|
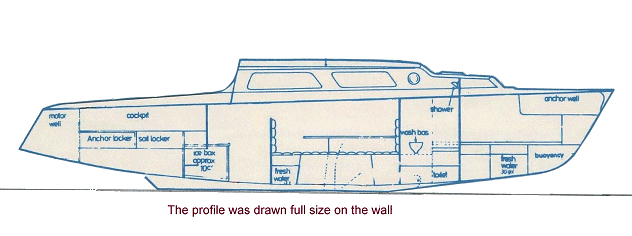
We wanted maximum facilities in the accommodation in a restricted hull space so that space had to be carefully utilised and the best way to
do this was to work on a full size drawings, so on a wall under the house we drew a full size profile and set out what we wanted to fit in.
At first it seemed that getting full head room was not going to be practical, no matter which way we drew it either the hull looked too
deep and clumsy, or the cabin sides looked too high. Finally we came up with a solution, we would create an optical illusion by giving the
deck a pronounced reverse sheer, but at the same time make the hull to deck join a slight concave line and as this would stand out in a
dark colour the space between the deck and gunwale would disappear, this also gave us more usable room inside.
Every thing on a sailing boat is a compromise, narrow beam had been forced on us by the road rules, so to compensate a smaller than usual
rig was needed together with a reasonable amount of ballast to make the boat positively self righting. To make the retractable keel
manageable half the required weight would have to be in the hull, and the best way seemed to be making the hull bottom solid up to the
interior floor level , this also would create an extremely strong base for the centre board I redrew the lines drawings several times
to achieve the desired amount of buoyancy under the water line and also achieve enough volume under the floor for the amount of ballast.
At first the floor space forward looked impossibly small, but after doing a mock up of the toilet- shower compartment it was adequate
as long as there was elbow room, and hopefully no one would have to spend much time in there.
An important decision had to be made regarding the centre board.
For a boat with off the beach capability I prefer a swing keel, provided that the case size does not intrude too much in too the
accommodation, but that compromise again! A long narrow keel is the most efficient but does upset the interior layout, it also
creates a lot of turbulence in the long case, and a raising mechanism is also a problem. I made up mock ups of several keel
arrangements; all had problems with a lifting gear. I wanted something that could be operated from the cockpit without messy
tackles and winches but still using manual power, so decided to try hydraulics, but again a problem, the longest suitable lifting
ram made in stainless steel only had a fifteen inch movement, and in the end this was the controlling factor in the final design.
11,000 grey cast iron was chosen for the keel. I had used it on the 24 and had found that, provided new Pig iron was used, it was ideal.
It was easy to work with, was resistant to corrosion, and Tar epoxy paint held well on it. It also appeared that there was very little
electrolysis between it and good grades of stainless steel.
Go back to Index | Go on to Next Episode
|
|